Comment se caractérise le travail de préparateur de
commande chez FM Logistic ?
C’est un métier difficile et exigeant physiquement. Les
préparateurs de commandes parcourent l’entrepôt pour construire
leur commande en allant chercher les différents colis dans les
racks. L’environnement de travail est contraignant avec le bruit,
la chaleur ou le froid, le rythme de travail soutenu comme
dans toutes les entreprises de la Supply Chain.
Les manutentions manuelles et le port sont la cause de 55% des
accidents du travail chez FM Logistic. Depuis plusieurs années,
nous travaillons sur l’amélioration des conditions de travail et
avons testé pratiquement tous les équipements d’aide à la
manutention disponibles sur le marché mais aucun ne
correspondait totalement à nos besoins. C’est pourquoi nous avons
décidé de développer notre propre dispositif de suppléance.
L’Université Technologique de Compiègne étant à proximité de
notre plateforme, un partenariat avec le département Biomécanique
Sport et Santé s’est mis en place pour travailler ensemble sur ce
projet.
C’est un projet ambitieux, sur quelle méthodologie vous
appuyez-vous ?
La méthodologie de projet se déroule en 3 étapes. Nous avons
débuté par une phase de cartographie de l’état de santé des
collaborateurs, puis nous avons travaillé sur le diagnostic,
enfin nous allons pouvoir passer à la conception du cahier des
charges fonctionnel qui sera soumis aux industriels susceptibles
de fabriquer le dispositif.
Lors de la première étape d’état des lieux, nous avons analysé
les données internes, réalisé une étude documentaire et
questionné tous les préparateurs de commandes. Il s’avère que 90%
des collaborateurs interrogés ressentent des douleurs lombaires.
L’analyse de l’accidentologie établit que les accidents du
travail concernent principalement le dos, les maladies
professionnelles sont liées elles aussi à des lésions du dos mais
aussi de l’épaule.
Pour analyser les mouvements des préparateurs de
commande, vous avez utilisé la technique de la motion capture.
Expliquez-nous.
Effectivement lors de la phase de diagnostic, nous voulions avoir
une analyse très fine des mouvements exécutés par les
préparateurs de commandes. Pour cela nous avons installé dans
l’entrepôt 18 caméras calibrées et synchronisées. Douze
préparateurs de commande ont été identifiés sur la base du
volontariat. Les préparateurs ont été sélectionnés sur la base de
facteurs individuels très différents en termes d’ancienneté,
genre, âge et poids. Ils ont été équipés de 70 marqueurs répartis
sur 15 segments du corps. Nous avons également travaillé sur
trois hauteurs différentes de prises de colis.
Les mouvements des opérateurs ont été enregistrés pendant 3 jours
pendant lesquelles nous avons reproduit des scénarios identiques
à leur journée de travail habituelle.
Dans un second temps, sur des journées complètes de travail, 10
collaborateurs ont porté un capteur muni d’un accéléromètre
capable de mesurer les flexions de dos et de les comptabiliser.
Nous avons également mesuré l’impact de la fatigue sur le
mouvement : travaille t’on de manière identique en début et en
fin de journée, le lundi et le vendredi ?
Quels enseignements avez-vous pu tirer de cette
expérience ?
Toutes ces données, et elles étaient nombreuses, ont été
analysées par Khalil Ben Mansour, Directeur du laboratoire de
Biomécanique et de Bioingénierie de l’UTC et l’équipe de la
Direction QHSE FM Logistic. Des éléments très importants en
termes de posturologie ont pu être mis en évidence. Ainsi nous
avons pu visualiser qu’un préparateur de commande fléchit son dos
à plus de 60° en moyenne 400 fois par jour. 40% des colis sont
pris à une hauteur favorisant des postures pénibles.
L’impact physique du travail est important, le
cardiofréquencemètre nous a permis de mesurer que l’activité
réalisée par un préparateur de commande est similaire à une
course à pied avec des temps de récupération souvent insuffisants
durant les temps de déplacement motorisés dans l’entrepôt. Tout
cela nous amène à réfléchir sur l’ensemble de l’organisation du
travail.
Nous avons également pu mettre en évidence des facteurs
protecteurs : le collectif de travail, la cohésion d’équipe et
l’entraide.
Quelle est la prochaine étape du projet ?
Le cahier des charges fonctionnel est pratiquement finalisé. En
dehors de l’aspect purement technique, le confort,
l’acceptabilité, et la praticité sont des critères extrêmement
importants. L’UTC travaille actuellement sur le prototype que
nous devrions pouvoir commencer à tester en avril. Nous
referons alors une session de motion capture. Nous devons
vérifier que le dispositif répond bien à toutes les
problématiques. Une fois cette étape validée, nous pourrons
passer en phase d’industrialisation et déployer ce nouveau
dispositif sur l’ensemble de nos unités logistiques.
Analyser le mouvement pour prévenir les TMS
En 2017, FM Logistic a lancé en partenariat avec l’Université Technologique de Compiègne une expérience innovante visant à concevoir un dispositif d’aide à la manutention totalement adapté aux besoins des préparateurs de commandes.Zoom
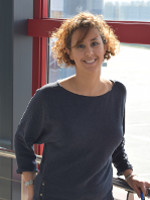
Samya BELLHARI TRAHIN
Ergonome & Psychologue du travail
Fm Logistic
- #Maladies Professionnelles
- 19/03/2018